Air Emissions Treatment Equipment
The CMM Group provides the design, installation, maintenance, and repair of air pollution control equipment that reduces environmental impact by destroying harmful volatile organic compounds (VOC) released during manufacturing processes. Our VOC emission control solutions include regenerative thermal oxidizers, recuperative thermal oxidizers, catalytic oxidizers, and rotary concentrators suited for a variety of applications.
Regenerative Thermal Oxidizer (RTO)
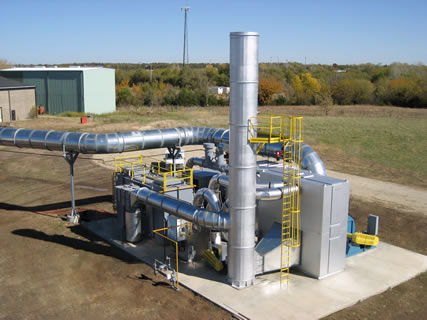
Recuperative Thermal Oxidizer
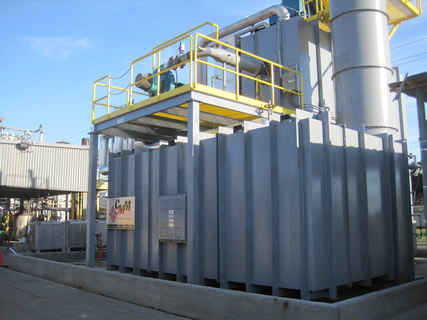
Catalytic Oxidizer
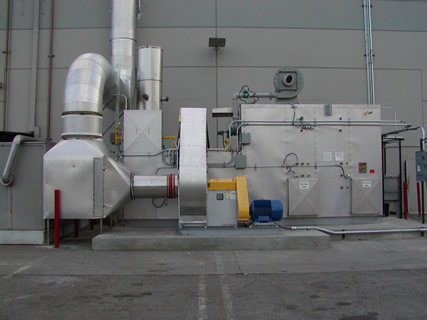
Rotary Concentrator
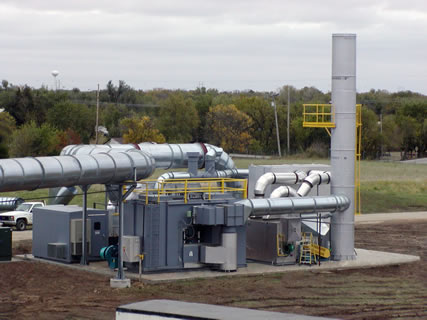
Energy Recovery
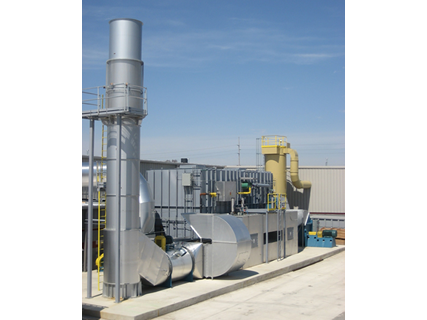