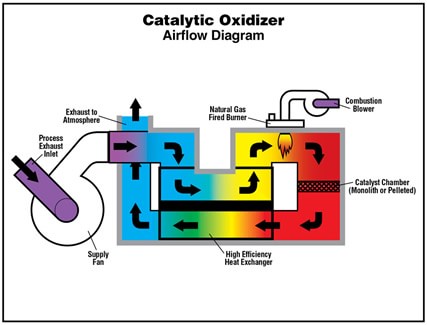
Catalytic Oxidizers
Highly Effective VOC Emission Control
Catalytic Oxidizers from The CMM Group are designed to destroy air pollutants and volatile organic compounds in air from process exhaust streams at temperatures ranging from 260°C (500°F) to 345°C (650°F). Catalytic oxidizers utilize a high-efficiency counter-flow plate type heat exchanger. Oxidation is achieved as VOC emissions pass through a heated bed of precious metal catalyst.
The basic design concept of catalytic oxidation is to utilize an industrial grade catalyst to promote the chemical reaction at lower temperatures as compared to thermal oxidation. The air pollutant is mixed with oxygen, heated to an elevated temperature and passed through a catalyst, thus destroying the pollutant in the air stream by converting it to CO2, H2O and heat. The rate of reaction is controlled by the temperature of the catalyst chamber and the amount of time that the pollutant spends within the catalyst itself. Catalytic oxidation commonly requires less energy to operate due to lower operating temperatures. Air pollutant destruction efficiencies of 99% can typically be guaranteed.
Catalytic Oxidizer – Video
Catalytic Oxidizer – Typical Applications
Common uses include:
- Converting web dryers
- Chemical processing
- Engine test facilities
- Food manufacturing
- Flexible packaging
- Heat-set printing
- Pharmaceutical manufacturing
- Many others…
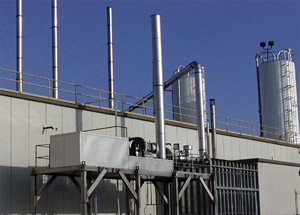
Catalytic Oxidizer – Advantages & Disadvantages
Advantages:
- Low operating costs with low air pollutant concentrations
- Low maintenance costs
- Ease of operation
- Ease of install
Disadvantages:
- High capital cost with stainless steel parts
- Potential for catalyst poisons
- Limited to moderate air pollutant concentrations
Catalytic Oxidizer – Standard Features
- High air pollutant destruction efficiencies are guaranteed
- Lowest operating costs available with energy efficient design
- Designed to meet your specific project requirements
- Proven high quality components are used throughout
- Control scheme is designed to automatically react to your
manufacturing process - Modern PLC based controls with color touch-screen interface
- Data-logger is included for recordkeeping
- Meets or exceeds all regulations
- 4,250 to 102,000+ NCMH
- (2,500 to 60,000+ SCFM)
- Suited for air streams with low to moderate levels of air pollutant
Request a Quote for Catalytic Oxidizers
Let us know how The CMM Group can assist you.
REQUEST A QUOTECatalytic Oxidizer Services
CMM provides expert catalytic thermal oxidizer service to ensure minimal downtime and maximum efficiency of your equipment. Our services include:
- PLC/HMI replacement
- Variable Frequency Drive (VFD) upgrade
- Oxidizer insulation repair/replacement
- Oxidizer media cleaning
- Preventative maintenance
- Spare & replacement parts
- Retrofits & relocation
How Does a Catalytic Oxidizer Work?
During operation, the process exhaust fumes are forced into the catalytic oxidizer inlet plenum (using a high pressure supply fan) and directed through the “cold” side of a high-efficiency, counter-flow plate type heat exchanger.
The VOC/HAP laden air then enters into the combustion chamber (typically at a temperature very close to that required for oxidation) where it is thoroughly mixed for temperature uniformity. To maintain set point temperature, auxiliary fuel is introduced if necessary. The preheated stream then passes through a fixed bed of industrial grade catalyst where air pollutant destruction takes place.
After passing through the catalyst chamber, the clean (hot) air is routed back through the “hot” side of the heat exchanger where it continuously preheats the incoming process air. Upon exiting the heat exchanger, the clean (cooled) air is routed to the atmosphere through an exhaust chamber and ultimately through the exhaust stack. Heat exchangers in standard catalytic units are typically fabricated of heavy-duty stainless steel. Thermal recovery efficiencies (TRE) range from 50% to 80%. Internal chambers of a catalytic oxidizer are manufactured entirely of heavy gauge stainless steel. Thermal expansion joints are incorporated where necessary. To maintain low external shell temperatures and minimize radiant heat loss, the internal chambers are covered with blanket insulation and then clad, typically with embossed aluminum.
Why Choose The CMM Group
- We provide turnkey, Single Source Solutions that minimize downtime, maximize productivity, save energy and reduce operating costs.
- Our professional staff has many years of design, fabrication and sales experience in a wide range of industries from Aerospace Parts to Wood Finishing.
- We’re committed to providing personalized, expert advice.
- We offer competitively priced solutions to a variety of equipment needs.
- We meet specific customer needs through all phases of project implementation while completing jobs on-time and within budget.
- We offer free support because we care about your site as much as you do.
What CMM Customers Say
“The hard work and dedication your team made this project a great success. I greatly appreciate that the installation went exactly as planned both time and budget wise, and that we were back in production with minimal disruption as promised. Additionally the efficiencies and energy savings have proven to be accurate and genuine.”-Satisfied customer,
Request a Quote for Catalytic Oxidizers & VOC Abatement Systems
Call (920) 336-9800 to let us know how The CMM Group can assist you.
REQUEST A QUOTE